Rigid-Flex PCB Fabrication Service
Capel's 15-year Rigid flexible printed circuit board technology expert team
-provide valuable insights and guidance to our customers;
-deep understanding of the technical aspects of rigid-flex circuit board technology enables them to offer solutions tailored to each customer's unique requirements.
-integrate cutting-edge technology and design principles into their products,ensures Capel's customers receive state-of-the-art rigid-flex circuit boards that meet or exceed industry standards.
Rigid-Flex PCBs production capacity can reach more than 70000sqm per month
--manage high-volume orders and meet tight production schedules. Whether you require small or large quantities, we can fulfill your order requirements promptly and efficiently.
Support customized 2-32 layer high-precision rigid flexible pcb circuit board
-advanced technology, equipment, and processes to ensure accurate and reliable production. Our attention to detail, stringent quality control measures, and comprehensive testing help us deliver high-quality rigid flexible PCBs that meet the highest industry standards.
Application Cases Of Rigid-Flex PCB Circuit Boards
Provide reliable solutions in manufacturing rigid-flex circuit boards for customers in the wearable devices, medical equipment, aerospace and defense systems, automotive systems, consumer electronics, industrial automation, and telecommunications.
-Customized rigid flexible PCBs that meet their specific requirements;
-Depending on your industry-specific needs, we can provide rigid flexible printed circuit boards with specialized materials such as high-temperature resistant materials for automotive and aerospace applications, as well as medical-grade materials for medical device applications. We also keep updated with the latest rigid-flex PCB manufacturing technologies to meet the evolving demands of these industries.
Rigid Flexible PCB Fabrication Process
1. Cutting: Cutting of hard board base material: Cut a large area of copper-clad board into the size required by the design.
2. Cutting the flexible board base material: Cut the original roll material (base material, pure glue, covering film, PI reinforcement, etc.) into the size required by the engineering design.
3. Drilling: Drill through holes for circuit connections.
4. Black hole: Use potion to make the toner adhere to the hole wall, which plays a good role in connection and conduction.
5. Copper plating: Plate a layer of copper in the hole to achieve conduction.
6. Alignment exposure: Align the film (negative) under the corresponding hole position where the dry film has been pasted to ensure that the film pattern can correctly overlap with the board surface. The film pattern is transferred to the dry film on the board surface through the principle of light imaging.
7. Development: Use potassium carbonate or sodium carbonate to develop the dry film in the unexposed areas of the circuit pattern, leaving the dry film pattern in the exposed area.
8. Etching: After the circuit pattern is developed, the exposed area of the copper surface is etched away by the etching solution, leaving the pattern covered by the dry film.
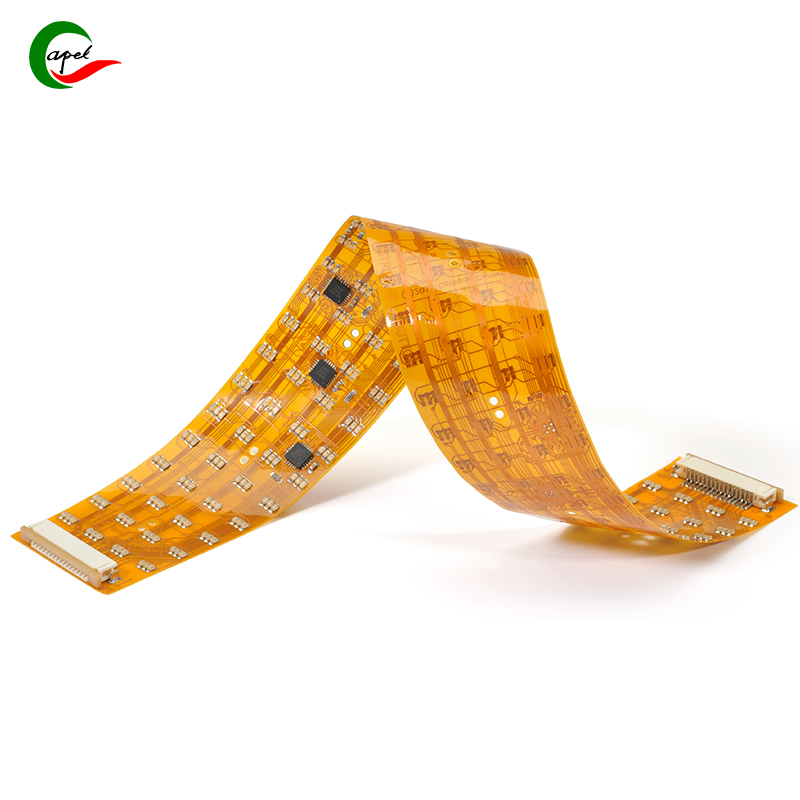
flex pcb assembly
9. AOI: Automatic optical inspection. Through the principle of optical reflection, the image is transmitted to the equipment for processing, and compared with the set data, the open and short circuit problems of the line are detected.
10. Lamination: Cover the copper foil circuit with an upper protective film to prevent circuit oxidation or short circuit, and at the same time function as insulation and product bending.
11. Laminating CV: Press the pre-laminated covering film and reinforced plate into a whole through high temperature and high pressure.
12. Punch: Use the mold and the power of the mechanical punch to punch the work plate into the shipping size that meets the customer's production requirements.
13. Lamination (superposition of rigid-flex pcb boards)
14. Pressing: Under vacuum conditions, the product is gradually heated, and the soft board and hard board are pressed together through hot pressing.
15. Secondary drilling: Drill the via hole connecting the soft board and the hard board.
16. Plasma cleaning: Use plasma to achieve effects that conventional cleaning methods cannot achieve.
17. Immersed copper (hard board): A layer of copper is plated in the hole to achieve conduction.
18. Copper plating (hard board): Use electroplating to thicken the thickness of hole copper and surface copper.
19. Circuit (dry film): Paste a layer of photosensitive material on the surface of the copper-plated plate to serve as a film for pattern transfer. Etching AOI wiring: Etching away all the copper surface except the circuit pattern, etching out the required pattern.
20. Solder mask (silk screen): Cover all lines and copper surfaces to protect the lines and insulate.
21. Solder mask (exposure): The ink undergoes photopolymerization, and the ink in the screen printing area remains on the board surface and solidifies.
22. Laser uncovering: Use a laser cutting machine to perform a specific degree of laser cutting on the position of the rigid-flex junction lines, peel off theflexible board part, and expose the soft board part.
23. Assembly: Paste steel sheets or reinforcements on the corresponding areas of the board surface to bond and increase the hardness of important parts of the FPC.
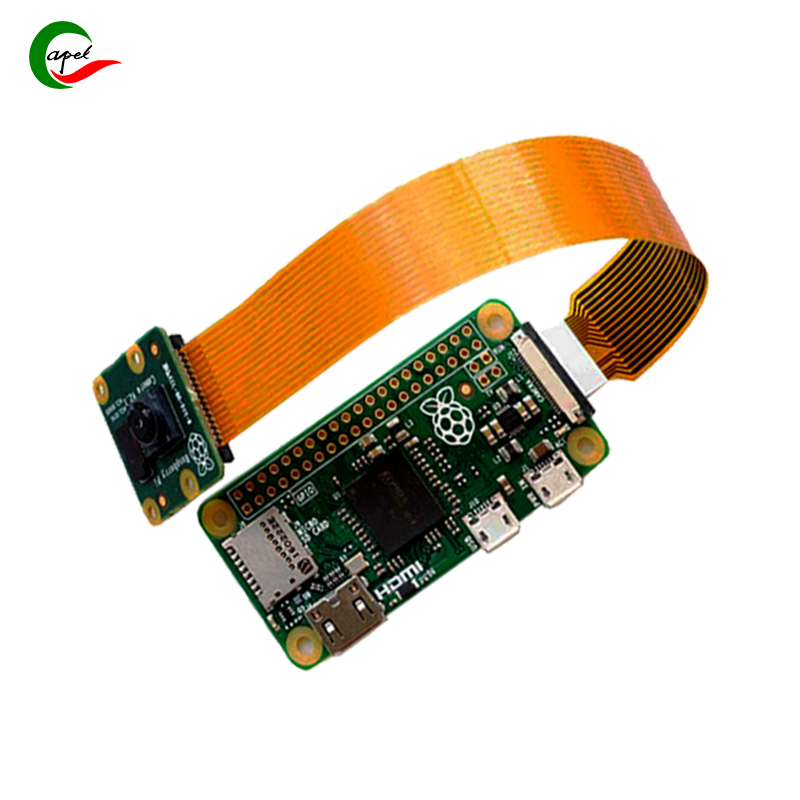
Rigid flexible pcb assembly
24. Test: Use probes to test whether there are open/short circuit defects to ensure product functionality.
25. Characters: Print marking symbols on the board to facilitate the assembly and identification of subsequent products.
26. Gong plate: Use CNC machine tools to mill out the required shape according to customer requirements.
27. FQC: The finished products will be fully inspected for appearance according to customer requirements, and defective products will be picked out to ensure product quality.
28. Packaging: The boards that have passed the full inspection will be packed according to customer requirements and shipped to the warehouse.
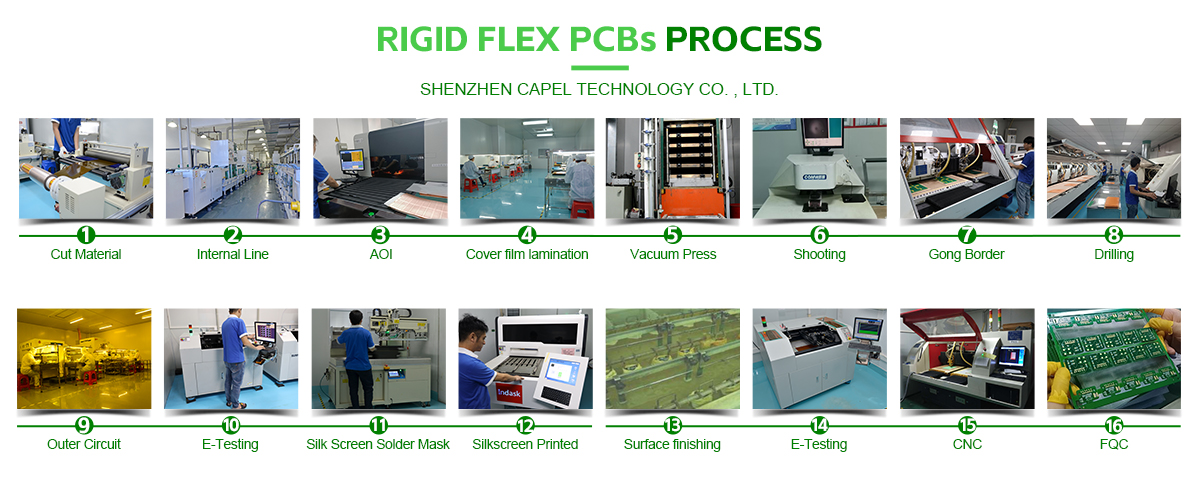
Turkey Rigid Flexible PCB Assembly
Provide expertise and assistance during the design phase, helping customers optimize their designs
for functionality, reliability, and cost-effectiveness;
Being able to produce small quantities of rigid-flex PCB prototypes in a timely manner, allowing customers to evaluate and validate their designs before proceeding with mass production;
Maintain detailed documentation throughout the assembly process, including bills of materials (BOMs), assembly instructions, and test records;
On-time delivery(Capel has efficient production planning, effective resource management, and close coordination with customers throughout the manufacturing process.);
Address any concerns or issues that may arise post-delivery and provide prompt technical support or warranty services if required.
Rigid Flexible PCB Fabrication Advantages
Fully automated and high-precision production equipment
-minimize human errors, improve efficiency, and enhance the overall quality of our rigid flex printed circuit boards.
Capel has its own R&D base, production factory, and patch factory for rigid-flex circuit boards
-continuous research and development to create innovative solutions and improve the performance of our customers products.
-Capel has full control over the manufacturing process, ensuring quality control and efficient production,has shorter lead times and faster delivery.
-Capel can handle repairs and modifications to the rigid-flex circuit boards they produce,provide after-sales support and ensure customer satisfaction.
Continuous innovation of excellent and advanced process technology
-We prioritize innovation and constant improvement in our rigid flexible PCB fabrication process,continuously explores and adopts new and advanced technologies,provide you with cutting-edge solutions and ensure that your rigid flexible PCBs boards meet the latest technical standards.
-Optimize the manufacturing process to improve efficiency and reduce costs,minimize material waste, shorten lead times, and offer cost-effective solutions to our customers.
Rigid Flexible PCB Production Capability
Category | Process Capability | Category | Process Capability |
Production Type | Single layer FPC flex PCB Double layers FPC flec PCB Multilayer FPC Aluminum PCB Rigid-Flex PCB |
Layers Number |
1-30 layers FPC Flexible PCB 2-32 layers Rigid-FlexPCB 1-60 layers Rigid PCB HDI Boards |
Max Manufacture Size |
Single layer FPC 4000mm Doublelayers FPC 1200mm Multi-layers FPC 750mm Rigid-Flex PCB 750mm |
Insulating Layer Thickness |
27.5um /37.5/ 50um /65/75um 100um /125um / 150um |
Board Thickness |
FPC0.06mm-04mm Rigid-Flex PCB025-60mm |
Tolerance of PTH Size |
+0.075mm |
Surface Finish |
Immersion Gold/mmersion Silver/Gold Plating /Tin Plating/OSP |
Stiffener | FR4 /PI/ PET /SUS /PSA/Alu |
Semicircle Orifice Size |
Min 0.4mm | Min Line Space width | 0.045mm/0.045mm |
Thickness Tolerance |
+0.03mm | Impedance | 500-1200 |
Copper Foil Thickness |
9um/12um /18um / 35um /70um/100um |
Impedance Controlled Tolerance |
+10% |
Tolerance ot NPTH Size |
+0.05mm | The Min Flush Width | 0.80mm |
Min Via Hole | 0.1mm | lmplement Standard |
GB/IPC-650/PC-6012IPC-01311/ IPC-601311 |
Certifications | ULand ROHS 5014001:2015 IS0 9001:2015 IATF16949:2016 |
Patents | model patents invention patents |
Quality Control for Rigid Flexible PCB Production
Complete quality control system
- We have implemented a comprehensive quality control system to ensure the highest standards in rigid flexible PCB production(material inspection, process monitoring, product testing, and evaluation)
Our operation is ISO 14001:2015 , ISO 9001:2015, IATF16949:2016 certified
-our commitment to quality management, environmental sustainability, and continuous improvement,our dedication to delivering reliable and high-quality rigid-flex circuit boards.
Our products are UL and ROHS marked
-ensures that our rigid flexible PCBs meet safety standards and comply with industry regulations,free from hazardous substances,make them environmentally friendly and safe for use in various applications
Obtained more than 20 utility model patents and invention patents
-our focus on developing unique and creative solutions in rigid flexible PCB manufacturing,Our commitment to innovation ensures that you receive cutting-edge products that meet your specific requirements.
Quick Turn Rigid-Flex PCB Prototyping
24-hour non-stop rigid flexible circuit board prototype production service
Delivery for small batch orders usually takes 5-7 days
Mass production delivery usually takes 10-15 days
Production | Number of layers | Delivery time (business days) | |||
Samples | Mass Production | ||||
FPC | 1L | 3 | 6-7 | ||
2L | 4 | 7-8 | |||
3L | 5 | 8-10 | |||
For FPC flexible PCBs with more than 3 layers, add 2 business days for each additional layer | |||||
HDI buried blind vias PCB and Rigid-Flex PCB |
2-3L | 7 | 10-12 | ||
4-5L | 8 | 12-15 | |||
6L | 12 | 16-20 | |||
8L | 15 | 20-25 | |||
10-20L | 18 | 25-30 | |||
SMT: Add an additional 1-2 business days to the above delivery time | |||||
RFQ:2 working hours CS:24 working hours | |||||
EQ:4 working hours Production capacity: 80000m/month |
Instant Quote for Flexible PCB and Flex PCB Assembly
Capel produces in its own factory and is controlled by a team of experts with 15 years of experience to ensure that every product is 100% qualified.